introdução
Como você pode perceber, hoje as coisas andam mudando muito rápido! Em plena globalização, no auge das voláteis transformações, a busca pela competitividade entre as empresas é uma constante. Nesta aula, abordaremos um conceito importantíssimo: Lean Manufacturing, um termo que designa uma filosofia de gestão desenvolvida pela japonesa Toyota, em 1950, e que tem por objetivo principal “enxugar” o processo produtivo ao eliminar operações que não agregam valor ao sistema. Também conhecido por “manufatura enxuta”, o Lean tem melhorado a eficiência operacional e qualidade de processos e produtos nos mais diversos tipos de negócios. Conhecer bem os princípios do Lean Manufacturing é essencial para aqueles que buscam ganho de produtividade, qualidade e desenvolvimento organizacional. Então, vamos aprender sobre essa metodologia imprescindível ao seu futuro profissional!
Bons estudos!
Origem da produção Lean
Conforme já dissemos na Introdução, o Lean Manufacturing foi desenvolvido no Japão, mais precisamente na Toyota, gigante automotiva que, atualmente, lida com inúmeras outras atividades, mas que foi inovadora na época em que o país estava arrasado e lutando para se reerguer após a avassaladora derrota na Segunda Guerra Mundial. Atribui-se a criação da filosofia Lean ao engenheiro Taiichi Ohno que, no pós Guerra Fria esteve à frente dos processos de fabricação da Toyota e liderou o desenvolvimento de uma metodologia de gestão focada na melhoria contínua e na eliminação de desperdícios. Daí surge o Sistema Toyota de Produção (do inglês, Toyota Production System – TPS) que se sustenta, principalmente, nos conceitos de Just in time e de Jidoka.
O Just in time (JIT), termo que significa “no tempo certo”, preconiza que o processo de produção aconteça sem estoques e com alto nível de qualidade. Daí supõe-se que nenhum produto deve ser fabricado/ofertado, transportado ou adquirido antes do tempo. O Jidoka, por sua vez, significa automação inteligente, “automação com toque humano” ou, ainda, autonomação. Baseia-se na ideia de um operador e/ou as máquinas terem a capacidade de detectar em tempo recorde a ocorrência de anormalidades e interromper toda a linha de produção automaticamente, evitando desperdícios.
Convém salientar que, inspirada no Sistema Toyota de Produção, a filosofia Lean foi desenvolvida e se tornou uma das principais responsáveis pela retomada exitosa da indústria japonesa, tornando-a, na época, uma referência global em qualidade. É verdade que, em seu nascimento, tal filosofia ou metodologia, como também é chamada, filha do TPS, ainda não tinha sido batizada por “Lean”, termo que surgiu pela primeira vez no livro The Machine that Changed the World, dos autores de Womack, Jones e Roos, obra que foi publicada nos Estados Unidos no início dos anos 90.
O livro foi fruto de estudos realizados pelo Massachusetts Institute of Technology (MIT) sobre a indústria automobilística no mundo (WOMACK; JONES; ROOS, 2004). A partir dessa literatura, o Lean Manufacturing, ou Produção Enxuta, entrou nos dicionários de quase, senão todos, os povos do mundo.
Assimile
A partir daí, sabe-se que, para que um sistema produtivo seja considerado enxuto (Lean), faz-se necessário que esteja comprometido com a fluidez dos produtos ao transitar pelas fases de transformação a que são submetidos, ou seja, os processos produtivos de agregação de valor devem ser ininterruptos e trabalhar sob um sistema puxado de produção. Desse modo, estando as atividades vinculadas à demanda, desenvolve-se a cautela de se manter a “linha de produção” abastecida somente com a quantidade de materiais/tempo precisamente dimensionados e necessários, atentando evidentemente ao fortalecimento cultural promotor da busca pela melhoria contínua (LIKER, 2005). Hoje, o Lean passou de uma filosofia/metodologia/sistema à condição primordial da sobrevivência de muitas organizações.
videoaula: Origem da produção Lean
No vídeo reforça-se, ainda que superficialmente, a origem do Lean e ressalta-se a amplitude dessa filosofia que, para o japonês, chega a ter o status de religião pela importância atribuída. Enfim, o objetivo do vídeo é trazer uma reflexão sobre o conteúdo que se inicia. i
Videoaula: Origem da produção Lean
Para visualizar o objeto, acesse seu material digital.
Conceitos e aplicações do sistema
Aqui, nos aprofundaremos no conceito de Lean Manufacturing, explicitando, inclusive, algumas aplicações dessa importante filosofia quando tratada como sistema de gestão. Já cientes de como tudo começou e de quando o Sistema Toyota pariu o “Lean Manufacturing” ou manufatura enxuta, avançamos em nossos estudos. Por questões de praticidade, chamaremos esse sistema apenas de Lean.
O conceito de Lean, como já discutido anteriormente, pauta-se na eliminação de desperdícios e tarefas sem valor agregado, com o intuito de reduzir custos e despesas, utilizando a menor quantidade de esforços, representados por equipamentos e humanos, na produção de bens e serviços sem defeitos, no menor tempo possível, aumentando, portanto, a satisfação dos clientes e a produtividade da empresa (OHNO, 1997).
A essência do Lean Manufacturing está na redução de, no mínimo, sete tipos de desperdícios, a saber: perdas por superprodução, perdas por espera, perdas por transporte, perdas por processo, perdas devido à fabricação de produtos defeituosos, perdas por estoque e perdas por movimento (WERKEMA, 2010). Tal filosofia ou sistema de gestão pode ser aplicado aos diversos tipos de empresas e nos mais variados produtos e serviços. Além da Toyota, grandes corporações, como Nike, Intel e a fabricante de máquinas norte-americana Carterpillar Inc. são cases de sucesso na utilização do Lean. A Figura 1 apresenta os 7 tipos de desperdícios do Lean.
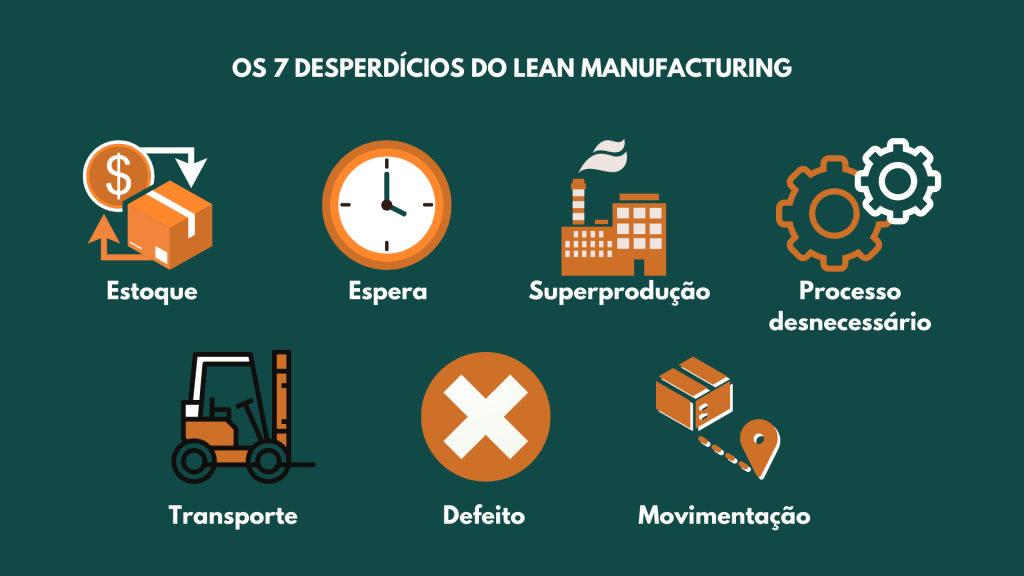
As perdas por estoque, sinteticamente, consistem na existência de grandes estoques de matérias-primas, material em processo e produto acabado, gerando elevados custos financeiros e em relação ao espaço físico. É sempre bom lembrar que estoque é capital imobilizado!
As perdas oriundas da espera dizem respeito ao tempo em que os trabalhadores e/ou as máquinas estão ociosos, ou seja, não estão produzindo. Grande parte desse tipo de desperdício pode ser resolvida com uma boa organização do layout e dos materiais que constam no espaço produtivo.
As perdas por superprodução podem ocorrer devido à produção excessiva ou pela produção antecipada em relação às necessidades dos estágios subsequentes da produção e do consumo (SHINGO, 1996).
De acordo com Antunes (2008), as perdas por processo são resultantes de atividades desnecessárias para que o produto ou serviço adquira suas características básicas de qualidade, visando à geração de valor para o cliente.
Sobre as perdas por transporte, Shingo (1996) defende que estão relacionadas diretamente a qualquer atividade de movimentação de materiais que geram custos e não agregam valor ao produto.
Segundo Antunes (2008), as perdas por fabricação de produtos defeituosos consistem na fabricação de peças e/ou produtos acabados fora da especificação de qualidade requerida pelo projeto, ou seja, que não atendem aos requisitos necessários de qualidade.
Por fim, as perdas por movimento consistem em movimentos desnecessários dos trabalhadores quando estão executando operações nas máquinas, nas linhas de montagem e em serviços.
Portanto, tendo conceituado o Lean, salienta-se que esse sistema é implementado quando se deseja aumentar a qualidade, reduzir desperdícios, obter ganhos de produtividade, desenvolver-se e se manter competitivo no mercado.
Videoaula: Conceitos e aplicações do sistema
O vídeo aborda, de modo geral, a importância em eliminar desperdícios e cita algumas possíveis soluções simples, baseadas nos conceitos já aprendidos. É importante salientar que existem os desperdícios puros (aqueles que devem ser eliminados) e os desperdícios necessários (aqueles que devem ser reduzidos e/ou tolerados). O primeiro tipo atrapalha. O segundo, por sua vez, agrega algum valor ao produto.
Videoaula: Conceitos e aplicações do sistema
Para visualizar o objeto, acesse seu material digital.
Principais princípios Lean
Chegamos ao terceiro e último bloco desta aula. Aqui, vamos falar sobre os princípios que permeiam o Lean. Vale considerar que princípios são alicerces, fundamentos e padrões a serem seguidos. Logo, depreende-se que os princípios do Lean formam a essência dessa filosofia ampla e crucial às organizações, e podem ser citados como os principais: definir valor, mapear os fluxos de valor, criar um fluxo contínuo, organizar um fluxo puxado (produção puxada) e buscar a perfeição (Figura 2).
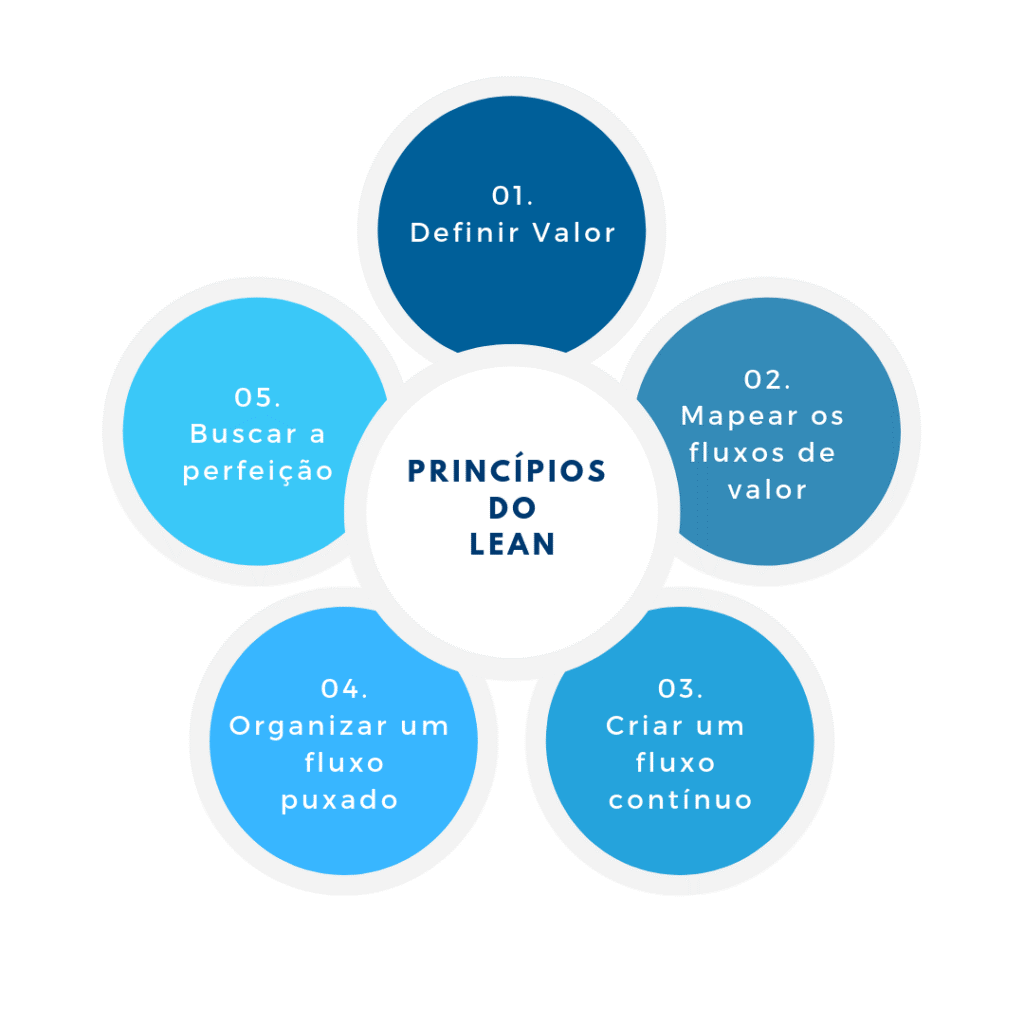
O princípio “definir valor” consiste justamente em analisar cada fase pela qual passa o produto e ver se ela agrega ou não valor. É importante sondar o que, de fato, o cliente deseja consumir, ou seja, definir o valor sob a ótica de quem compra para eliminar etapas que nada acrescentam ao bem ou serviço. Entenda que valor e preço são conceitos diferentes! Sugiro que você faça uma pesquisa e perceba cada definição, pois nem tudo que tem valor tem preço e vice-versa.
Mapear fluxo de valor: uma vez tendo definido o valor, faz-se necessário identificar a frequência, local e os principais tipos de barreiras que dificultam atender às necessidades do cliente. O objetivo é mapear todo o fluxo do valor, analisá-lo criticamente e verificar onde se pode melhorar a fim de torná-lo mais eficiente (MARTINS, 2020).
Fluxo contínuo: a instituição de um fluxo contínuo consolida-se quando é possível reduzir atividades, esforços, tempos e custos, redesenhando e/ou introduzindo-se novos processos e/ou tecnologias. O fluxo contínuo é capaz de reduzir desperdícios e agregar valor ao produto (MARTINS, 2020).
Sistema de puxado: o lema é só produzir quando houver demanda. Tal metodologia consiste em controlar a produção a partir dos processos internos, também denominados subprocessos ou clientes que se comportam ora como clientes, ora como fornecedores, ao longo de toda a cadeia produtiva em que só se produz o que for demandado. Destarte, o sistema de produção puxada tenta reduzir ou eliminar os excessos. A lógica é que nada venha a ser produzido pelo “subprocesso fornecedor” sem que o “subprocesso cliente” tenha solicitado (MARTINS, 2020).
Buscar a perfeição: é uma busca contínua. Quando se busca a perfeição sempre há algo que pode ser melhorado. A lógica é: hoje, preciso ser melhor que ontem. Para que essa perfeição chegue, todos os níveis envolvidos no processo precisam estar engajados na busca pela excelência nos processos (MARTINS, 2020).
É importante frisar que a implementação da filosofia Lean conta com uma série de ferramentas e técnicas que são utilizadas objetivando-se a maximização da qualidade e a minimização ou eliminação de desperdícios ou atividades que constam no fluxo e não agregam valor (LÉXICO LEAN, 2003). Tais princípios tornam o Lean uma metodologia eficaz a ser considerada por toda organização que deseja fazer mais com menos.
videoaula: Principais princípios Lean
O vídeo destaca a importância da construção de uma cultura Lean em que todos os colaboradores, do nível estratégico ao operacional, estejam comprometidos e inteirados sobre os benefícios do sistema japonês. Salienta-se que a implantação bem sucedida dessa filosofia requer união de propósitos e perseverança.
Videoaula: Principais princípios Lean
Para visualizar o objeto, acesse seu material digital.
Estudo de caso
A fábrica Pezão, situada no município de Terra do Nunca, no estado do Sol Quente, atua no segmento de calçados, desde 1900. Mais precisamente, sua produção concentra-se em sandálias simples. Durante a pandemia da Covid-19, as vendas despencaram e a empresa passou a ter sérios problemas. Constatou-se, nesse período, uma quantidade enorme de matéria-prima e de sandálias em estoque. Na sala de não conformidades, havia muitas sandálias defeituosas e, notoriamente, muita gente ociosa no chão de fábrica. O Sr. Sérgio, proprietário da empresa, convidou-o para ajudá-lo a resolver os problemas de sua organização e lhe confidenciou que estava com pouquíssimos recursos para investimentos.
Utilizando os conceitos já apreendidos em nossa aula sobre Lean Manufacturing, ajude, na medida do possível, seu Sérgio e a fábrica Pezão a resolverem seus problemas.
Resolução do Estudo de Caso
Reflita sobre tudo que você já aprendeu sobre o Lean Manufacturing e relacione possíveis soluções para o estudo de caso. Esteja à vontade para associar a essência do Lean ao problema enfrentado por seu Sérgio na empresa Pezão. O vídeo, intitulado Estudo de caso, traz uma reflexão e dicas sobre como pensar e resolver a problemática.
Resolução do Estudo de Caso
Para visualizar o objeto, acesse seu material digital.
Saiba mais
Artigo sobre desempenho operacional
Leia o artigo intitulado Análise da relação entre manufatura enxuta e desempenho operacional de empresas do setor automotivo no Brasil para compreender um pouco mais sobre o Lean e sua implementação no setor automotivo.
JABBOUR, A. B. L. S. Análise da relação entre manufatura enxuta e desempenho operacional de empresas do setor automotivo no Brasil. Revista de Administração, FEA - USP. São Paulo, v. 48, n. 4, p. 843-856, out.-dez., 2013.
Vídeo sobre a história da Toyota
O vídeo apresenta a história da Toyota, desde os tempos da fabricação de teares até os dias atuais.
Automação, Just in Time, Poka Yoke, Desperdícios, e Kanban são alguns dos temas abordados.
PARTE I - TOYOTA - Lean Manufacturing. Praticantelean. YouTube. 6’50’’.